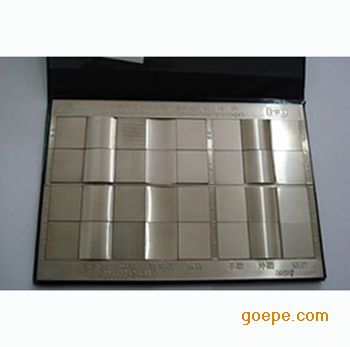
表面粗糙度比较样块选型表
表面粗糙度比较样块
表面粗糙度比较样块是检查加工后工件表面的一种对比量具,它的使用方法是以样块工作面的表面粗糙度为标准,凭触觉(如手摸)或视觉(可借助放大镜、比较显微镜等)与待检查的工件表面进行比对,从而判别别检查表面的表面粗糙度是否合乎要求。这是一种定性的检查工具。
用比较样块比对的方法虽简便、快速、经济实用,但只能定性测量,无法得到表面粗糙度的定量值。比较法要求检验者具有丰富的实践经验。因此,比较法用于具有一般而不是严格要求的表面粗糙度的零件表面。
为了统一比较样块的制造与使用,保证比较样块的准确度和质量要求,我国相继发布了六项比较样块的国家标准,现在分别进行介绍:
一、铸造表面粗糙度比较样块:
铸造表面长期被人们认为是很粗糙的表面,所以对其表面粗糙度一般不加以控制与评定,设计者在零件图上对铸造表面只标注不加工符号。但随着铸造加工工艺的发展及铸造表面质量的不断提高,对铸件表面粗糙度的控制与评定引起有关行业和部门的重视。设计者根据功能要求在图样上规定了铸造表面粗糙度要求。评定铸造表面粗糙度时,*好的方法是样块比较法。
GB/T6060.1-1997《表面粗糙度比较样块 铸造表面》规定了铸造金属表面粗糙度比较样块的特征,该样块用来与它表征的合金材质和铸造方法相同的,并经过适当方法(如喷丸、喷砂、滚筒等方法)清理的铸件表面,通过视觉和触觉进行比较,评定铸造表面的粗糙度。标准的比较样块还可作为特定铸造工艺和铸件表面粗糙度选用的参考依据。
铸造表面粗糙度比较样块是表征特定合金材质和铸造方法的已知表面轮廓算术平均偏差Ra或微观不平度十点高度Rz值的样块。按铸造类型、合金种类、铸造方法所能达到的粗糙度数值分类,并规定了它的结构尺寸及标志。
样块的分类及参数值
铸造表面比较样块按铸造工艺及材质的不同分成两大类共15种
二、样块的制造方法
1、样块应按下列方法制造:
1)用电铸法复制的表面阳模;
2)用塑料或其他材料复制的表面阳模;
3)直接用表征的合金材质和铸造方法制造的表面。
2、复制样块用的原始母模的表面,必须体现要表征的特定铸造金属及合金材质和铸造方法的粗糙度特征的真实铸件表面(允许采用喷丸、喷砂、滚筒清理等适当方法清理),并且符合规定的表面粗糙度参数值。
三、样块的表面特征
1、样块表面应呈现它所要表征的特定铸造金属及合金材质和铸造方法产生的铸造表面粗糙度特征,而不应含有表面粗糙度以外的其他表面特征(尽管这些特征可能是实际铸件表面所允许存在的),如波纹度、缺陷等。
2、样块表面的色泽,应是它所表征的特定铸造金属及合金材质铸件表面所能出现的色泽。
加工办法 |
规格 |
Ra值 um |
每组块数 |
车外园 磨外园 刨 平磨
镗内孔 平铣 端铣 研磨 |
组合式 |
6.3.3.2 1.6-0.012 |
32 |
车外园 磨外园 |
双组式 |
6.3、3.2、1.6、0.8 |
8 |
刨 平磨 |
双组式 |
6.3-0.8 |
8 |
平铣 端铣 |
双组式 |
6.3-0.1 |
8 |
镗内孔 磨内孔 |
双组式 |
0.1-0.012 |
8 |
手研 机研 |
双组式 |
6.3-0.8 |
8 |
车外园 |
单组式 |
6.3-0.8 |
4 |
刨 |
单组式 |
6.3-0.8 |
4 |
镗内孔 |
单组式 |
6.3-0.8 |
4 |
锉 |
单组式 |
6.3-0.8 |
4 |
平铣 |
单组式 |
6.3-0.8 |
4 |
端铣 |
单组式 |
6.3-0.8 |
4 |
研磨 |
单组式 |
0.8-0.1 |
4 |
平磨 |
单组式 |
0.8-0.1 |
4 |
磨内孔 |
单组式 |
0.8-0.1 |
4 |
磨外园 |
单组式 |
0.8-0.1 |
4 |
手研 |
单组式 |
0.1、0.05、0.025、0.012 |
4 |
机研 |
单组式 |
0.1-0.012 |
4 |
线切割 |
单组式 |
1.6、2.5、3.2、5.0、6.3 |
5 |
电火花 |
单组式 |
0.4、0.8、1.6、3.2、6.3、12.5 |
6 |
抛光 |
单组式 |
0.8、0.4、0.2、0.1、0.012、
0.015、0.025 |
7 |
铸造钢铁砂型 |
单组式 |
3.2、6.3、12.5、25、50、
100、Rz800、1000 |
8 |
抛喷丸 |
单组式 |
0.2、0.4、0.8、1.6、3.2、
6.3、12.5、25、50、100 |
10 |
喷砂 |
单组式 |
0.8、1.6、3.2、6.3、12.5、25 |
6 |
详细参数如下:
表面粗糙度比较样板 组合式:0.8、1.6、3.2、6.3 32 GB6060.2-85
表面粗糙度比较样板 镗内孔:0.8、1.6、3.2、6.3
表面粗糙度比较样板 刨:0.8、1.6、3.2、6.3
表面粗糙度比较样板 平铣:0.8、1.6、3.2、6.3
表面粗糙度比较样板 端铣:0.8、1.6、3.2、6.3
表面粗糙度比较样板 磨外圆:0.1、0.2、0.4、0.8
表面粗糙度比较样板 平磨:0.1、0.2、0.4、0.8
表面粗糙度比较样板 研磨:0.1、0.05、0.025、0.012
表面粗糙度比较样板 电火花线切割:0.63、1.25、2.5、5.0、10 GB6060.3-86
表面粗糙度比较样板 电火花:0.4、0.8、1.6、3.2、6.3、12.5 GB6060.3-86
表面粗糙度比较样板 抛光:0.8、0.4、0.2、0.1、0.05、0.025、0.012 GB6060.4-88
表面粗糙度比较样板 铸造钢铁砂型:3.2、6.3、12.5、25、50、100、800、1000 GB6060.1-85
表面粗糙度比较样板 抛喷丸:0.2、0.4、0.8、1.6、3.2、6.3、12.5、25、50、100 GB6060.5-88
表面粗糙度比较样板 喷砂:0.8、1.6、3.2、6.3、12.5、25
表面粗糙度比较样块
表面粗糙度比较样块是检查加工后工件表面的一种对比量具,它的使用方法是以样块工作面的表面粗糙度为标准,凭触觉(如手摸)或视觉(可借助放大镜、比较显微镜等)与待检查的工件表面进行比对,从而判别别检查表面的表面粗糙度是否合乎要求。这是一种定性的检查工具。
用比较样块比对的方法虽简便、快速、经济实用,但只能定性测量,无法得到表面粗糙度的定量值。比较法要求检验者具有丰富的实践经验。因此,比较法用于具有一般而不是严格要求的表面粗糙度的零件表面。
为了统一比较样块的制造与使用,保证比较样块的准确度和质量要求,我国相继发布了六项比较样块的国家标准,现在分别进行介绍:
一、铸造表面粗糙度比较样块:
铸造表面长期被人们认为是很粗糙的表面,所以对其表面粗糙度一般不加以控制与评定,设计者在零件图上对铸造表面只标注不加工符号。但随着铸造加工工艺的发展及铸造表面质量的不断提高,对铸件表面粗糙度的控制与评定引起有关行业和部门的重视。设计者根据功能要求在图样上规定了铸造表面粗糙度要求。评定铸造表面粗糙度时,*好的方法是样块比较法。
GB/T6060.1-1997《表面粗糙度比较样块 铸造表面》规定了铸造金属表面粗糙度比较样块的特征,该样块用来与它表征的合金材质和铸造方法相同的,并经过适当方法(如喷丸、喷砂、滚筒等方法)清理的铸件表面,通过视觉和触觉进行比较,评定铸造表面的粗糙度。标准的比较样块还可作为特定铸造工艺和铸件表面粗糙度选用的参考依据。
铸造表面粗糙度比较样块是表征特定合金材质和铸造方法的已知表面轮廓算术平均偏差Ra或微观不平度十点高度Rz值的样块。按铸造类型、合金种类、铸造方法所能达到的粗糙度数值分类,并规定了它的结构尺寸及标志。
样块的分类及参数值
铸造表面比较样块按铸造工艺及材质的不同分成两大类共15种
二、样块的制造方法
1、样块应按下列方法制造:
1)用电铸法复制的表面阳模;
2)用塑料或其他材料复制的表面阳模;
3)直接用表征的合金材质和铸造方法制造的表面。
2、复制样块用的原始母模的表面,必须体现要表征的特定铸造金属及合金材质和铸造方法的粗糙度特征的真实铸件表面(允许采用喷丸、喷砂、滚筒清理等适当方法清理),并且符合规定的表面粗糙度参数值。
三、样块的表面特征
1、样块表面应呈现它所要表征的特定铸造金属及合金材质和铸造方法产生的铸造表面粗糙度特征,而不应含有表面粗糙度以外的其他表面特征(尽管这些特征可能是实际铸件表面所允许存在的),如波纹度、缺陷等。
2、样块表面的色泽,应是它所表征的特定铸造金属及合金材质铸件表面所能出现的色泽。